In the oil and gas, chemical, and power industries, pressure control, flow regulation, and system isolation of fluids are critical to ensuring the safe operation of equipment. For procurement managers responsible for sourcing precision components in sectors such as oil and gas, petrochemicals, power generation, and industrial automation, understanding how instrument valves work is essential. However, many buyers lack a clear understanding of how these components function and the differences between various types of valves.
Instrument valves are primarily used to regulate flow, isolate instruments, and relieve pressure within pipeline systems. They serve as mechanical control points that allow operators to start, stop, or throttle the flow. These valves enable safe calibration, inspection, and maintenance without having to shut down the entire process system. Due to their reliability and precision, they are essential in high-pressure and hazardous environments.
When selecting or evaluating valves for procurement, it’s crucial to understand how the internal mechanism of the valve works and how each type responds under operational conditions.
What Are Instrument Valves and Why Use Them?
Instrument valves, sometimes referred to as gauge valves or isolation valves, are used to control the flow to pressure, flow, or temperature measurement instruments. They are typically installed between the process medium and the instrument and perform the following functions:
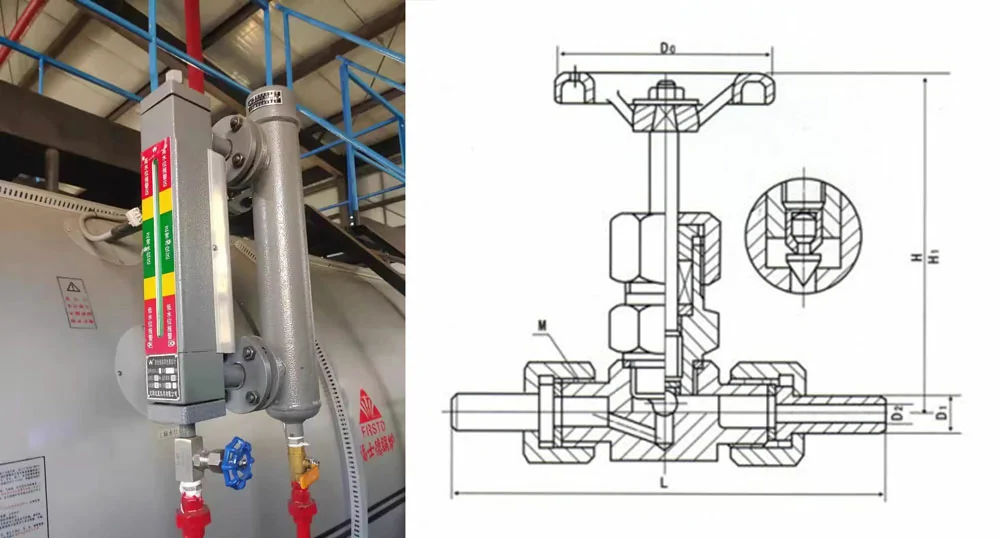
- Isolate the instrument during shutdown or maintenance
- Vent air or gas from the system before measurement
- Control the flow rate to sensitive instruments
- Redirect flow using manifolds
Instrument valves are most commonly used in control panels, distribution skids, gas sampling systems, and analyzer shelters.
How Do the Internal Mechanisms of Instrument Valves Work?
The core functionality of an instrument valve lies in its precise control over the on/off state and flow rate of fluids or gases. This function depends on the internal valve mechanism. Although different types of instrument valves have different structures, their internal mechanisms generally consist of the following key components: valve body, valve stem (or disc), valve seat, sealing elements, valve rod, and actuating handle or actuator.
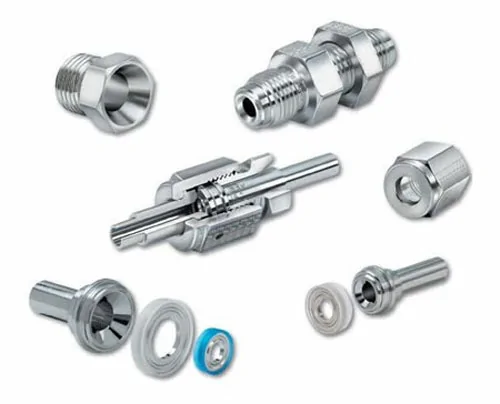
Below are the working principles of several common valve types
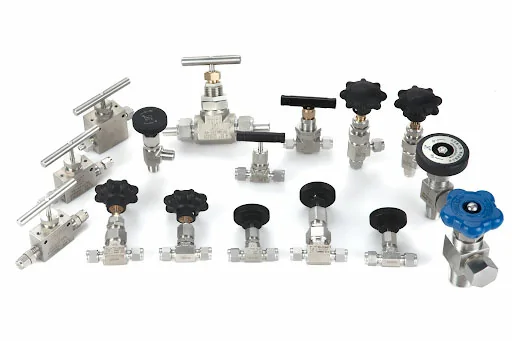
Válvula de agulha
Needle valves use a slender, tapered needle-shaped stem that fits into a matching valve seat. When the handle is rotated, the needle advances to gradually close the flow path. This design allows precise control of fluid flow, especially in low-pressure or low-flow systems.
Válvula de esfera
Ball valves consist of a spherical ball with a central bore. When the handle is rotated 90 degrees, the bore aligns with the flow path, allowing fluid to pass through. Rotating the handle again closes the flow. These valves are known for their durability and quick shutoff capability, making them ideal for isolating instruments.
Válvula de retenção
Check valves are designed for one-way flow. When fluid flows in the correct direction, the valve opens automatically; when backflow pressure is detected, the valve closes. Internally, check valves typically use a spring-loaded disc or ball—forward flow pushes the element open, while reverse pressure seals it shut.
Metering Valve
Metering valves are precision flow control devices that allow very fine adjustments. They usually feature finely threaded stems and are used in analytical instruments, blending systems, or any application requiring repeatable flow control.
Types of Instrument Valves and Their Working Principles
Different applications require different types of valves. Below is a classification of commonly used instrument valves in industrial environments:

- Needle Valve: Allows precise flow adjustment, suitable for applications requiring gradual and accurate control.
- Ball Valve: Suitable for quick shutoff; less precise but highly durable and widely applicable.
- Check Valve: Prevents backflow, commonly used in gas or liquid service lines to protect instruments.
- Metering Valve: Provides fine flow control in analytical applications.
- Double Block and Bleed Valve: Allows isolation and venting from a single valve body, reducing potential leak paths.
- Manifold Valve: Combines multiple valves into a single valve block for a compact and efficient control setup.
Depending on the application, each valve comes with specific pressure ratings, temperature tolerances, and body material options.
How Do Instrument Valves Work from a Physical Perspective?
From a fluid mechanics perspective, instrument valves control flow characteristics—such as pressure, velocity, and direction—by changing the cross-sectional area of the pipeline. Core physical principles involved include:
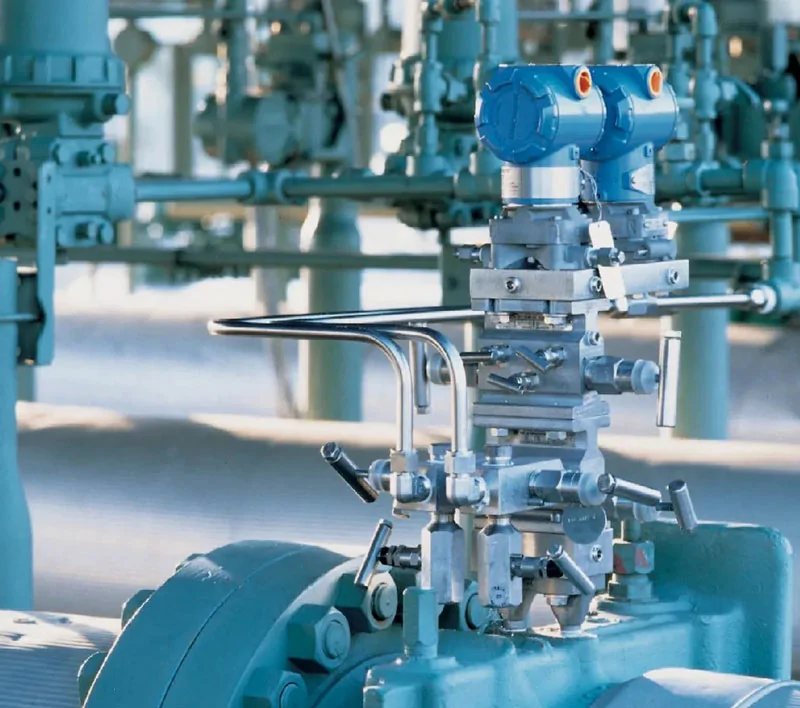
- Bernoulli’s Principle: As cross-sectional area decreases, flow velocity increases, causing pressure to drop accordingly.
- Laminar and Turbulent Flow: Valve designs aim to minimize turbulence and promote smooth flow to prevent vibration and wear.
- Backpressure and Flow Resistance: Valves introduce flow resistance, and the internal design determines the pressure drop across the valve.
Understanding these dynamics is critical when specifying valves for systems where flow rate, pressure stability, and temperature control are vital.
How Do Valves Operate in High-Pressure Systems?
In high-pressure systems (e.g., 6,000 PSI and above), instrument valves must meet specific engineering standards. Considerations include:
- Material Selection: Commonly uses 316 stainless steel, Alloy 400, or duplex stainless steel for high pressure and corrosion resistance.
- Seal Types: Typically requires metal-to-metal or reinforced PTFE seals to prevent leakage.
- Testing: Valves should undergo hydrostatic testing and certification to meet international standards (API, ISO, PED).
Selecting valves that meet the system’s pressure requirements is crucial for plant safety and process reliability.
At Waltervalves, all instrument valves undergo in-house testing at our 3,000-square-meter facility in China. Each high-pressure valve we ship is accompanied by complete documentation to ensure global compliance and safety.
Why Choosing the Right Instrument Valve Manufacturer Matters
Procurement decisions impact operational efficiency, maintenance planning, and plant safety. Sourcing from a trusted valve manufacturer ensures:
- Consistent quality control from raw materials to finished products
- Access to inventory for urgent orders
- Customization options for pressure ratings, threads, or end connections
- Technical support tailored to installation and application needs
Headquartered in China, Waltervalves serves customers in Southeast Asia, the Middle East, Europe, and North America. We specialize in manufacturing high-precision instrument valves, including needle valves, manifold valves, check valves, and metering valves. With factory-direct pricing, fast lead times, and strong export support, we are a strategic partner for bulk buyers.
Summary
Understanding how instrument valves function helps procurement managers make informed choices that impact system safety, performance, and cost. Whether you’re sourcing for a refinery, analytical lab, or chemical skid system, selecting the right valve and manufacturer is essential. Waltervalves offers reliable, factory-direct solutions to meet your needs.