In industrial manufacturing systems, strict and precise control of production processes is essential. Instrumentation valves play a foundational role in regulating the flow of fluids and gases. From isolation and throttling to venting and backflow prevention, they ensure stable process measurements and protect instrumentation components.
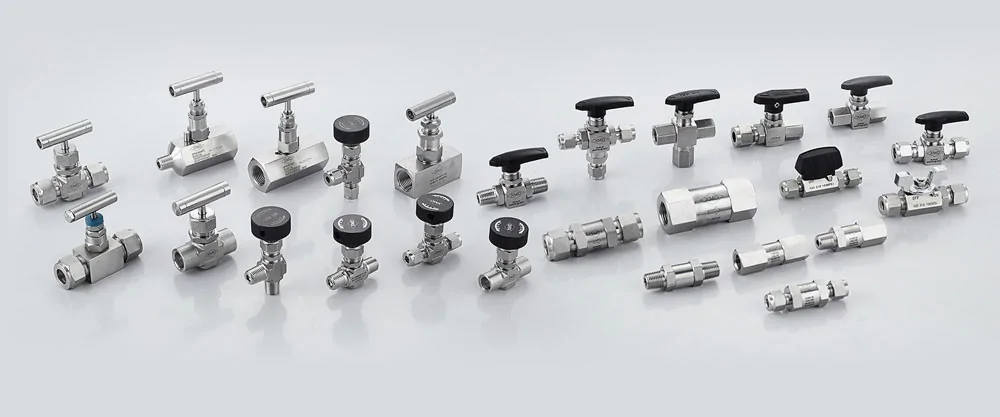
There are ten main types of instrumentation valves, each designed for specific control and measurement applications. These include ball valves, needle valves, globe valves, check valves, manifold valves, relief valves, vent valves, block and bleed valves, plug valves, and diaphragm valves. Each valve serves distinct functions such as flow control, pressure isolation, backflow prevention, and safe venting.
Understanding the different types of instrumentation valves is crucial for engineers, system designers, and procurement teams. Choosing the wrong type can compromise system integrity and create safety risks.
What Is an Instrumentation Valve?
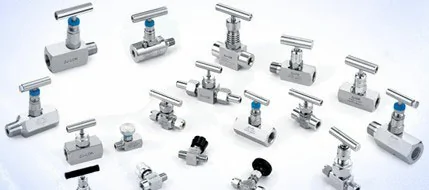
An instrumentation valve is a mechanical component used to control, isolate, regulate, or redirect the flow of fluids or gases within an instrumentation system. Unlike large process valves, instrumentation valves are typically compact and highly precise, making them suitable for applications requiring high accuracy and fast response.
These valves are usually installed near measuring instruments such as pressure gauges, transmitters, flow meters, and sampling lines. They are a critical part of measurement and control systems, ensuring the accuracy of instrumentation.
Why Classifying Instrumentation Valves Matters
Classifying instrumentation valves helps system engineers and buyers make informed decisions. Each valve type has a unique use—from precisely controlling gas flow to preventing backflow or relieving excess pressure.
Incorrect use of valves can lead to inaccurate measurements, decreased system efficiency, or even equipment damage. Understanding each valve’s type and how it works helps industries maintain system integrity, reduce maintenance downtime, and optimize operating costs.
Principais tipos de válvulas de instrumentação
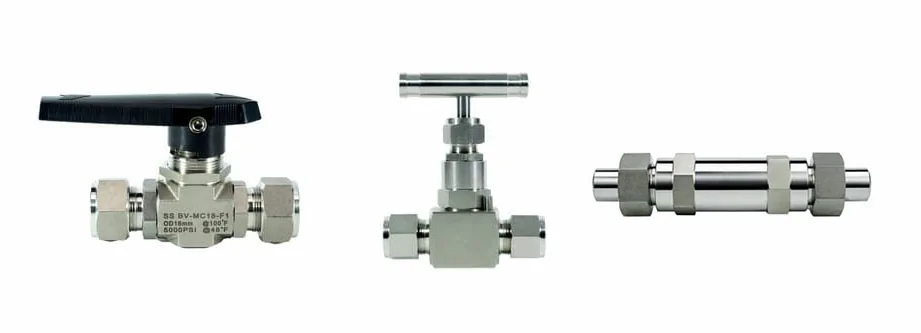
Válvulas de esfera
Ball valves are one of the most commonly used instrumentation valves due to their simplicity and high reliability. They use a hollow rotating ball to control flow. When the ball’s hole aligns with the pipe, fluid flows freely; when turned 90 degrees, flow is shut off.
Key Features:
• Quick quarter-turn operation
• Low pressure drop
• Durable and easy to operate
Typical Applications:
• Isolating pressure instruments
• Sampling systems
• Hydraulic and gas systems
Our ball valves are made of corrosion-resistant stainless steel, feature a compact body, and are leak-tested for high-pressure systems.
Válvulas de agulha
Needle valves are designed for precise flow control. They use a slender needle-shaped plunger that gradually enters or exits a small seat to finely adjust flow.
Key Features:
• Fine control of flow rate
• Ideal for low-volume, high-pressure applications
• Compact and durable
Common Uses:
• Calibration lines
• Analytical instruments
• Gas and liquid sampling
Our needle valves have high-pressure ratings, reliable stem seals, and various connection options for tight installations.
Válvulas globo
Globe valves regulate flow through a linear-motion disk. They are typically used in applications requiring flow adjustment rather than full open/close control.
Key Features:
• Excellent throttling capability
• Higher pressure drop than ball valves
• Suitable for frequent operation
Used In:
• Pressure control loops
• Temperature control systems
• Steam and utility lines
Our globe valves are precision-machined and built for long service life, suitable for both high- and low-pressure applications.
Válvulas de retenção
Check valves ensure fluid flows in only one direction. They open under forward pressure and close automatically under reverse pressure to prevent backflow.
Key Features:
• Passive (non-actuated) operation
• Prevents contamination and damage
• Available in ball and piston designs
Aplicativos:
• Instrument backflow protection
• Natural gas distribution systems
• Pumps and compressors
We produce compact, corrosion-resistant check valves designed for reliable performance in challenging environments.
Manifold Valves
Manifold valves are multi-port valves used to isolate, balance, or relieve pressure from devices like differential pressure transmitters. Multiple valves (2, 3, or 5) are combined into a single compact unit.
2-valve sets: isolation and venting
3-valve sets: isolation, equalizing, and venting
5-valve sets: additional venting and isolation for complex systems
Aplicativos:
• Pressure transmitter calibration
• Flow meter installation
• Gas distribution panels
Our manifolds are known for tight sealing, modular design, and easy installation, widely used in power and chemical industries.
Válvulas de alívio
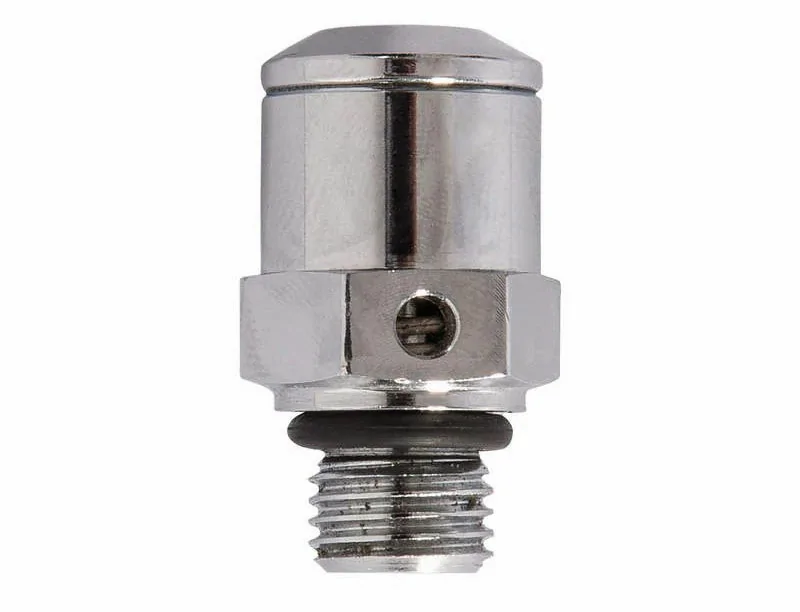
Relief valves are safety devices that protect instruments from overpressure. They open at preset pressures to safely release excess media.
Key Features:
• Spring-loaded or diaphragm-actuated
• Prevent pressure-related failures
• Often required by safety standards
Used In:
• Gas panels
• Pressure regulators
• Chemical injection systems
Our relief valves are factory-calibrated and tested to precise pressure settings to avoid unnecessary system shutdowns.
Vent Valves
These valves control the release of trapped pressure or air from instrumentation systems.
Functions:
• Safely vent gases before disassembly
• Remove residual air pockets
• Maintain drain systems
Aplicativos:
• Instrument calibration
• Shutdown procedures
• Pressurizing sample bottles
Vent valves from Walter Valve are robust and hand-tightened for tool-free operation.
Block and Bleed Valves
These specialized valves allow both isolation (blocking) and safe pressure release (bleeding) in a single unit.
Benefits:
• Increased maintenance safety
• Reduced need for multiple installations
• Saves space and installation time
Uses:
• Pressure transmitters
• Flow monitoring systems
• Oil and gas skid-mounted equipment
Walter Valve’s block and bleed designs are compact, corrosion-resistant, and highly reliable.
Plug Valves
Plug valves are often used in low-pressure applications. They use a cylindrical or conical plug to provide fast, accurate control.
Vantagens:
• Minimal flow restriction
• Compact size
• Quick operation
Used For:
• Sample collection
• Non-critical shut-off operations
Diaphragm Valves
Diaphragm valves use a flexible membrane to control flow. They are ideal for sterile, corrosive, or slurry applications where cleanliness is critical.
Benefits:
• Zero atmospheric leakage
• Easy to clean and sanitize
• No internal cavities
Industries:
• Pharmaceuticals
• Biotechnology
• Food processing
We offer custom diaphragm valve options for specialty applications requiring high hygiene and chemical resistance.
Materials and Connection Variants
Not all valves are the same. That’s why we offer:
- Material options: SS304, SS316, Monel, brass, Hastelloy, and more
• Connection types: Threaded (NPT/BSP), welded, flanged, compression (OD fittings)
Each configuration is tailored to system pressure, media compatibility, and installation space.
Walter Valve Solutions:
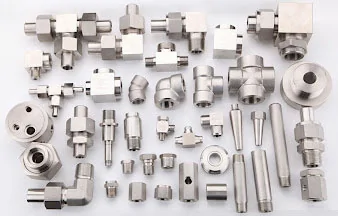
Specialized Valve Accessories and Customization Valve Accessories
Walter Valve manufactures a variety of valve accessories, including:
• Adapters
• Compression fittings
• Locking handles
• Tube connectors
These components ensure smooth, safe integration into broader systems and comply with ISO, DIN, and ANSI standards.
How Walter Valve Meets Industry Demands
Walter Valve provides factory-direct B2B solutions for industries that require high-precision, durable instrumentation valves. Our core strengths include:
• Factory pricing: competitive wholesale rates
• Ample inventory: key valve types in stock
• Short lead times: quick response for urgent orders
• Custom engineering: valve configurations tailored on request
We serve global and domestic clients in power generation, oil & gas, petrochemicals, water treatment, and manufacturing.
Conclusão
From ball and needle valves to relief, vent, and manifold valves, instrumentation valves are essential to every control and monitoring system. They help maintain measurement accuracy, ensure operational safety, and improve process efficiency.
Understanding the different valve types and when to use each is key to optimizing system design.
As a trusted B2B manufacturer with a long history in instrumentation valve production, Walter Valve offers not only a wide product range, but also technical guidance, custom engineering, and timely delivery to meet the evolving needs of modern industry.
Chamada para ação
Ready to upgrade your instrumentation system?
Contato info@waltervalves.com now to get catalogs, technical consultation, or wholesale pricing for your next project.
Let Walter Valve be your trusted partner in precision flow control.