At first glance, the two may seem similar, and it’s easy to confuse them in industrial control systems. However, instrumentation valves and instrument manifolds differ significantly in both structure and function. In the evolving field of industrial instrumentation, precision and control are paramount.
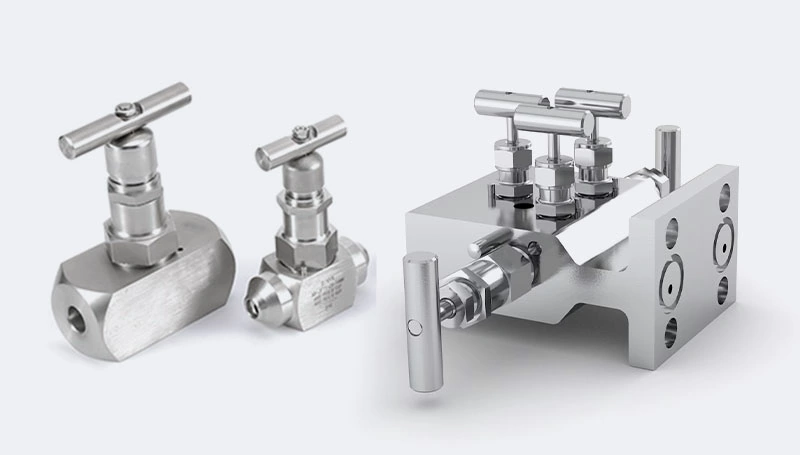
Instrumentation valves are not the same as instrumentation manifolds. An instrumentation valve is a single valve used to isolate or vent pressure instruments (such as gauges or transmitters). An instrument manifold—also known as a valve manifold—is a modular assembly composed of multiple valves, designed for more complex measurement and control systems, especially in differential pressure setups. While both are used with instruments, they serve different purposes.
This article explores classic use cases of each component and analyzes the differences between the two. It aims to clearly distinguish them and provide clarity for anyone navigating the complex world of instrumentation valves.
Understanding Gauge Valves
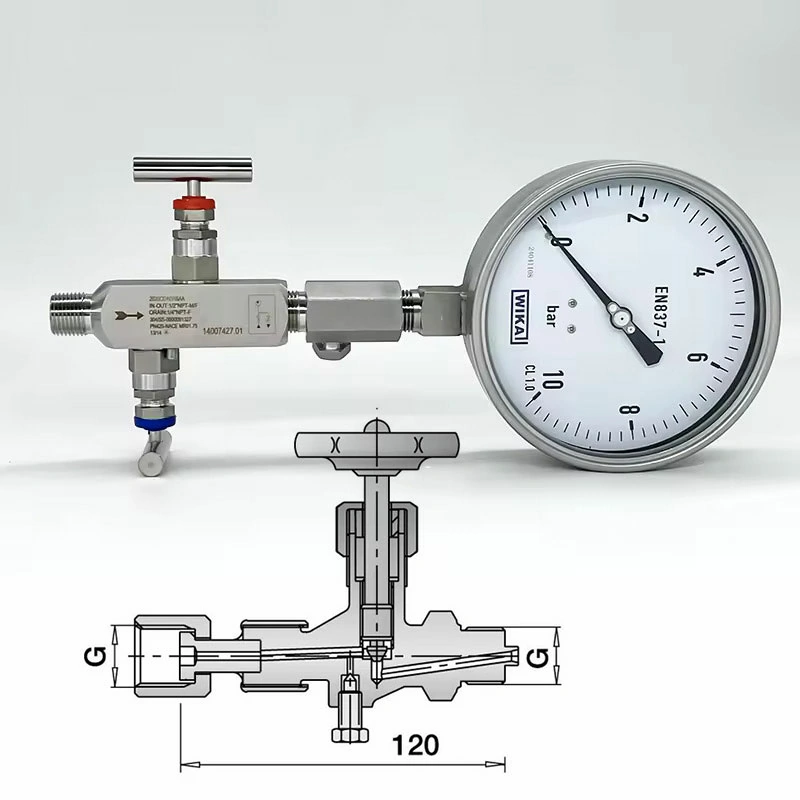
Válvulas de instrumentação are indispensable for connecting pipelines to instruments. They are used to isolate, vent, or calibrate pressure instruments. They allow controlled opening and closing of pressure gauges, making it easier to service or replace downstream instruments. Some instrumentation valves include drain ports to release pressure and drain the line during replacement.
Instrumentation valves are typically needle-type valves designed for fine control of fluid flow. The structure includes a valve body, stem, bonnet, and handle. Their compact size and simple mechanism make them ideal for space-constrained installations.
Exploring Instrument Manifolds
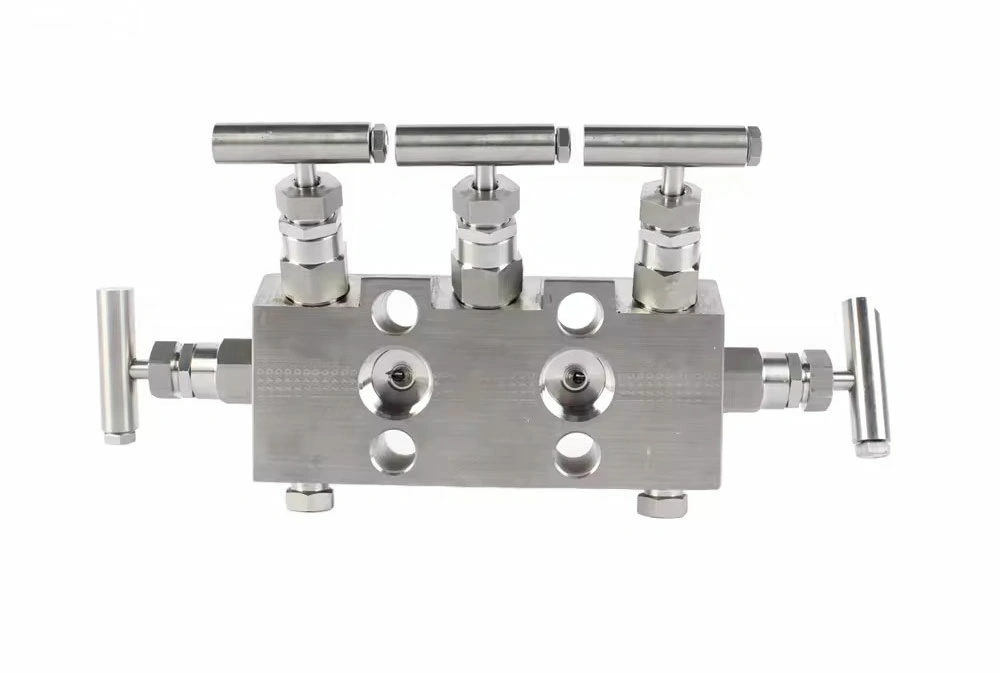
An instrument manifold integrates multiple instrumentation valves into a composite valve assembly. This allows multiple precision instruments (such as pressure or differential pressure transmitters) to be connected and controlled more efficiently. Manifolds provide more comprehensive and flexible isolation, equalization, and venting in process systems. Common types include 2-valve, 3-valve, and 5-valve manifolds.
- 2-valve manifolds: isolation and venting
- 3-valve manifolds: adds equalization for differential pressure systems
- 5-valve manifolds: includes two isolation valves, one equalizing valve, and two vent/test valves for added calibration and maintenance features
Instrument manifolds are suitable for broader system control applications. They are designed for multi-function operations without disrupting the primary process flow, offering operational flexibility—especially in complex industrial environments.
Differences Between Instrumentation Valves and Manifolds
Although both are used with instruments in pipelines, they differ notably in structure and function.
- Função: Instrumentation valves are simpler and provide isolation or pressure control for a single instrument. Manifolds offer integrated functions like isolation, equalization, venting, and draining.
- Estrutura: A gauge valve controls a single flow path using basic mechanisms like needle, ball, or globe designs. In contrast, a manifold contains multiple interconnected valves within one body.
- Aplicativo: Gauge valves are suited for basic setups to protect individual pressure instruments. Manifolds are used in more complex, high-precision, and safety-critical automation processes.
Comparison Table: Instrumentation Valve vs. Instrument Manifold
Recurso | Gauge Valve | Instrument Manifold |
Estrutura | Single valve, typically needle type | Multi-valve assembly (e.g., 2, 3, or 5 valves) |
Primary Function | Isolation, venting, calibration | Isolation, equalizing, venting, testing |
Suitable Instruments | Pressure gauges, transmitters | Differential transmitters, flow meters |
Installation Complexity | Simple, straightforward | More complex, multifunctional |
Maintenance Convenience | Easy to replace, low maintenance | Longer cycles, multifunctional support |
Typical Use Cases | Basic pressure measurement points | Differential systems, process control points |
Control Complexity | Low | Alta |
Flow Paths | Single | Multi-path (inlet, outlet, vent) |
Common Materials | Stainless steel, brass | High-grade stainless steel, special alloys |
Cost | Lower | Higher |
Importance in Process Control
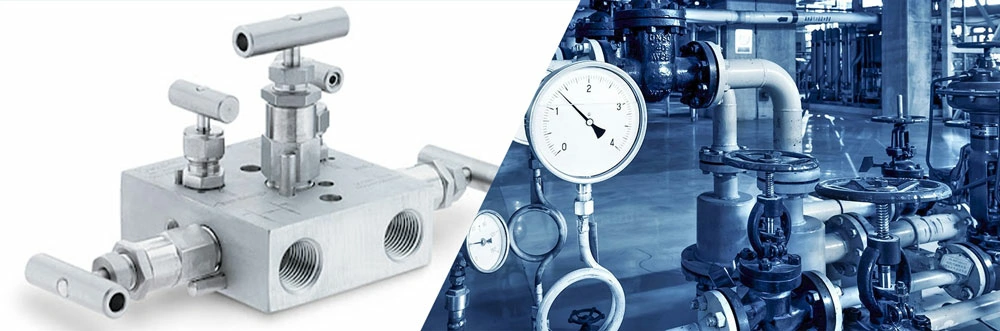
Instrumentation valves and manifolds are more than just connectors—they are critical to ensuring system safety and stability. In practice, both components help prevent leakage, ensure accurate data collection, and support multifunctional control. They meet modern industrial demands for safe, intelligent, efficient, and accurate operations.
In industries with high safety requirements—such as petrochemicals, power, and natural gas—they provide engineers with greater control precision and emergency response capabilities. Walter Valve is committed to serving process control systems with high-performance, reliable products that help customers build safer and more energy-efficient automation solutions.
Pressure Ratings and Performance
When selecting an instrumentation valve or manifold, pressure ratings and performance specifications are key considerations to match demanding conditions. Depending on the application, pressure requirements vary. Instrumentation valves typically operate within 3000 psi to 6000 psi. In harsher environments, manifolds may need to withstand ultra-high pressures.
In addition to pressure resistance, valves and manifolds must offer excellent sealing, corrosion resistance, and temperature adaptability. Walter Valve’s instrumentation valves are widely made from high-grade stainless steel (like SS316) or carbon steel, offering mechanical strength and corrosion resistance. They maintain tight sealing and responsive operation under extreme temperatures (from -40°C to +230°C).
Industrial Use Case: Petrochemical Industry
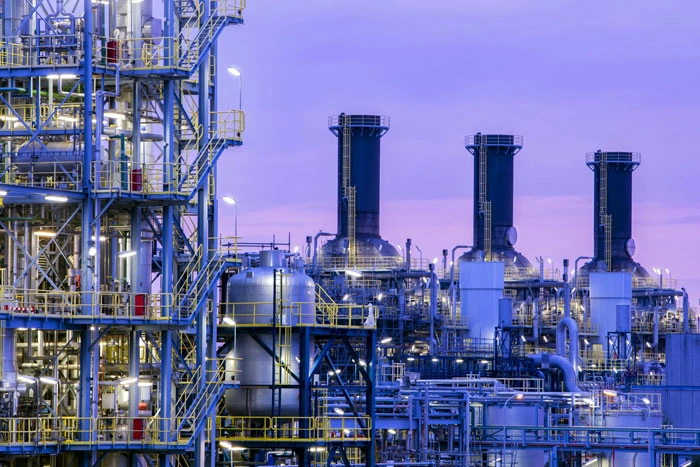
The petrochemical sector is among the most demanding for valve technology. Complex chemical processes, corrosive media, and extreme temperature variations place high demands on valve performance, particularly pressure resistance and corrosion protection.
In refining and natural gas processing, instrumentation valves are used to connect pressure transmitters and differential flow meters, ensuring precise media control and safe isolation.
In crude oil distillation units, 3- or 5-valve manifolds connect differential transmitters and other precision instruments to enable real-time, accurate data collection, online pipeline monitoring, automatic alarms, and safe venting and calibration.
Válvula Walter products are widely adopted in major refineries, LNG terminals, and chemical plants. They help customers ensure measurement accuracy while improving system safety and reliability. With short lead times, stable performance, and flexible configuration, we help reduce downtime risks and enhance operational stability.
Conclusão
For engineering projects, understanding the differences between instrumentation valves and manifolds is key to designing safer and more efficient systems. While both are widely used in industrial measurement and control, they differ fundamentally in structure, function, and application. The former focuses on single-point isolation and simple control; the latter integrates multiple functions and system connectivity—especially essential in high-precision scenarios.
If you have any questions about valve selection, inventory, or technical specifications, feel free to contact our engineering consultants at info@waltervalves.com.
PERGUNTAS FREQUENTES
Can instrumentation valves and manifolds be used interchangeably?
Not recommended. They differ significantly in structure and function. Valves are for simple measurement points; manifolds are for multi-function, differential applications.
What systems are manifolds best suited for?
Primarily for high-precision systems like differential pressure transmitters and dual-pressure flow meters, offering isolation, equalizing, and venting.
Does Walter Valve support custom products?
Yes. We customize according to your technical parameters, including port size, pressure rating, material, and more.
How do I determine the correct pressure rating?
Base it on the maximum working pressure of your process and apply a safety factor to select a model rated above that pressure.
Are the products compliant with international standards?
Yes. Walter Valve products meet ASME, ANSI, ISO, and other standards, with third-party certifications.
What is the typical lead time?
We maintain ample inventory. Standard models ship in 3–5 days; custom models typically take 7–15 days.